China’s Copper Mold Miracle: Halving Costs and Emissions with Groundbreaking Reuse Tech
How a Chinese Factory’s Innovation Delivers 50% Savings for Industry—and a Blueprint for Sustainable Manufacturing
On January 23, CWC visited a quiet corner of China’s industrial heartland, where engineers have unlocked a game-changing innovation that could redefine global manufacturing: a copper mold repair technology that cuts costs by 50% for end users while slashing CO2 emissions and waste. By reviving worn-out molds with nickel alloy layers up to 5 cm thick—without heat, without toxins, and with performance surpassing new materials—this breakthrough proves that sustainability and profitability can go hand in hand.
At the forefront of bringing this revolutionary solution to global industries is China West Connector (CWC). As an exclusive partner, CWC is enabling industries worldwide to access this cutting-edge technology, transforming both operational efficiency and environmental impact in manufacturing.
The Copper Mold Crisis and a Radical Solution
Copper molds, essential for shaping everything from steel beams to EV battery components, degrade rapidly under extreme heat and pressure. Replacement costs are staggering, and traditional repair methods like welding or plating fail to restore their original strength. This Chinese factory’s solution? A room-temperature process that rebuilds rather than replaces.
Key Innovations:
Ambient-Temperature Deposition: Unlike heat-based methods that warp or crack molds, this process bonds nickel alloy to copper at room temperature, ensuring zero thermal stress.
Unlimited Thickness: Layers of 1–5 cm (or more) are deposited seamlessly, bypassing the micron-scale limits of traditional plating.
Atomic Fusion: The new and original metals mix at a molecular level, eliminating adhesion issues and creating a unified structure stronger than pure copper.
Emission Cuts: Data from the World-Wide Fund for Nature (WWF) reveals the process slashes coal use by 80% (from 3,000 kg to 600 kg per ton of copper) and reduces CO2 emissions by 6,000 kg per ton (from 7,500 kg to 1,500 kg).
Why Traditional Methods Can’t Compete
Traditional repairs rely on heat-intensive techniques like welding or thin, fragile electroplating. These methods often weaken molds further, require frequent rework, and generate hazardous waste. By contrast, this factory’s technology eliminates heat distortion, delivers centimeter-thick coatings, and replaces toxic chrome plating with eco-friendly nickel alloy. The result? Molds that aren’t just repaired—they’re upgraded to last indefinitely.
Environmental Impact: A Sustainability Leap Backed by Data
The World-Wide Fund for Nature (WWF) reveals a staggering transformation in sustainability with this new copper mold repair technology. Traditional processes for producing 1 ton of copper plate molds consume 3,000 kg of coal and emit 7,500 kg of CO2. In stark contrast, the innovative process requires just 600 kg of coal and generates only 1,500 kg of CO2—an impressive 80% reduction in both energy use and emissions, saving 6,000 kg of CO2 per ton.
This breakthrough not only slashes energy consumption but also eliminates the environmental harm caused by toxic chrome plating. By replacing it with a safe nickel alloy and extending mold lifespans from 5–10 cycles to indefinite, the technology delivers a sustainable and eco-friendly alternative.
Traditional vs. Revolutionary: A Side-by-Side Comparison
Metric | Traditional Process | New Technology |
---|---|---|
Coal Consumption | 3,000 kg per ton | 600 kg per ton (80% less) |
CO2 Emissions | 7,500 kg per ton | 1,500 kg per ton (80% less) |
Mold Lifespan | 5–10 cycles | Indefinite |
Toxicity | Chrome plating harms ecosystems | Nickel alloy = safe alternative |
This revolutionary solution is not just a leap forward in manufacturing efficiency but also a game-changer for environmental responsibility.
A New Era of Industrial Resilience
This Chinese factory’s innovations aren’t just about cheaper repairs—they’re redefining manufacturing’s future. By turning molds into immortal assets, slashing costs, and eliminating waste, it offers a blueprint for sustainable, competitive industry.
This factory’s success is emblematic of a new era in Chinese manufacturing—one where innovation meets pragmatism. For industries battling inflation and sustainability mandates, such partnerships offer more than cost savings: they provide a lifeline to future-proof competitiveness.
As the factory’s CEO remarked, “We’re not here to replace Western manufacturing. We’re here to make it stronger.”
A Sustainable Future with CWC
CWC’s collaboration with this innovative Chinese factory is a testament to its commitment to sustainable manufacturing solutions. By enabling global industries to access this technology, CWC is helping companies achieve cost efficiency, improved performance, and a smaller environmental footprint.
As manufacturing evolves, CWC continues to be a trusted partner in delivering cutting-edge innovations that redefine what’s possible.
With the CWC bridging trust gaps, that vision is now within reach.
Ready to transform your supply chain?
Explore CWC’s solutions today
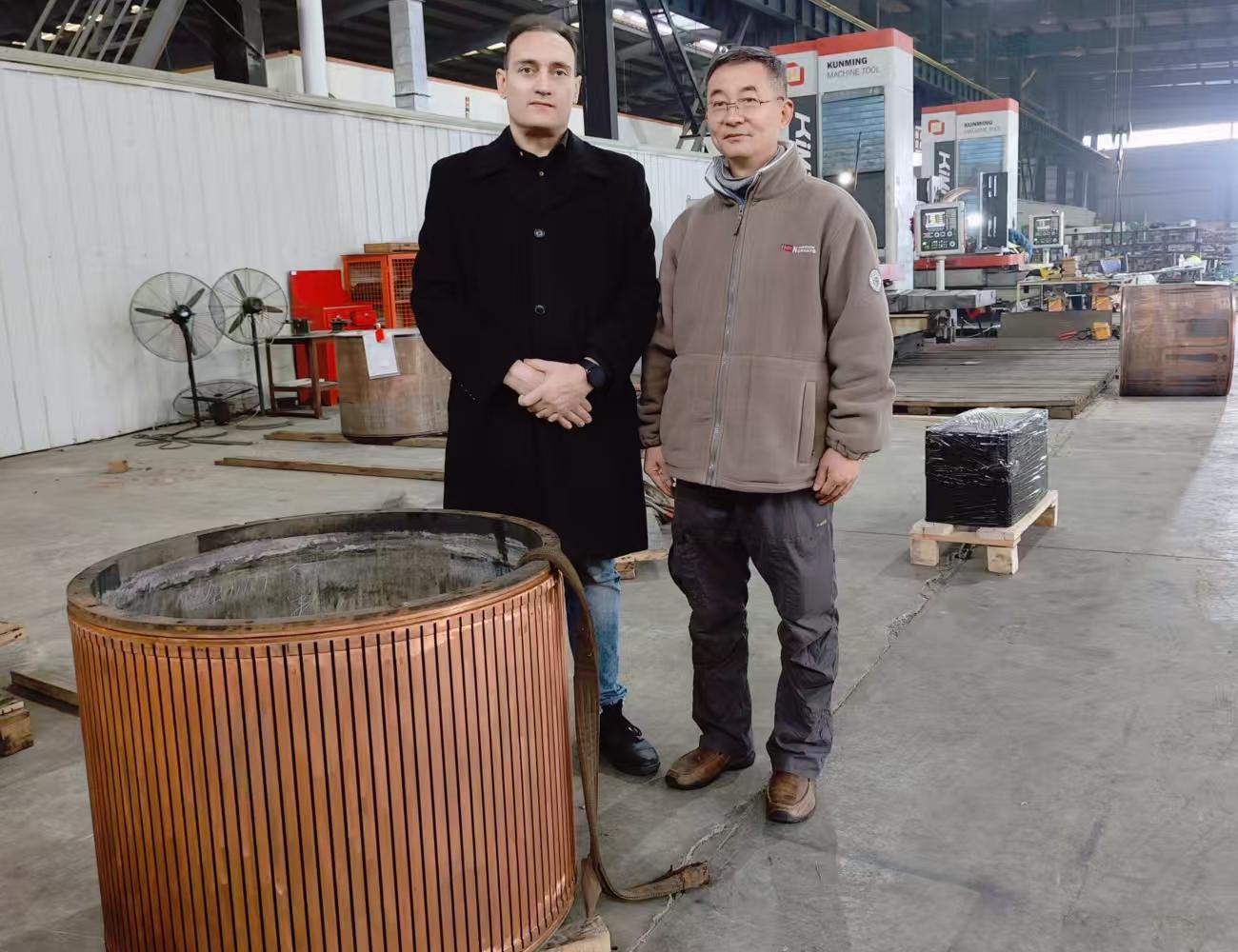
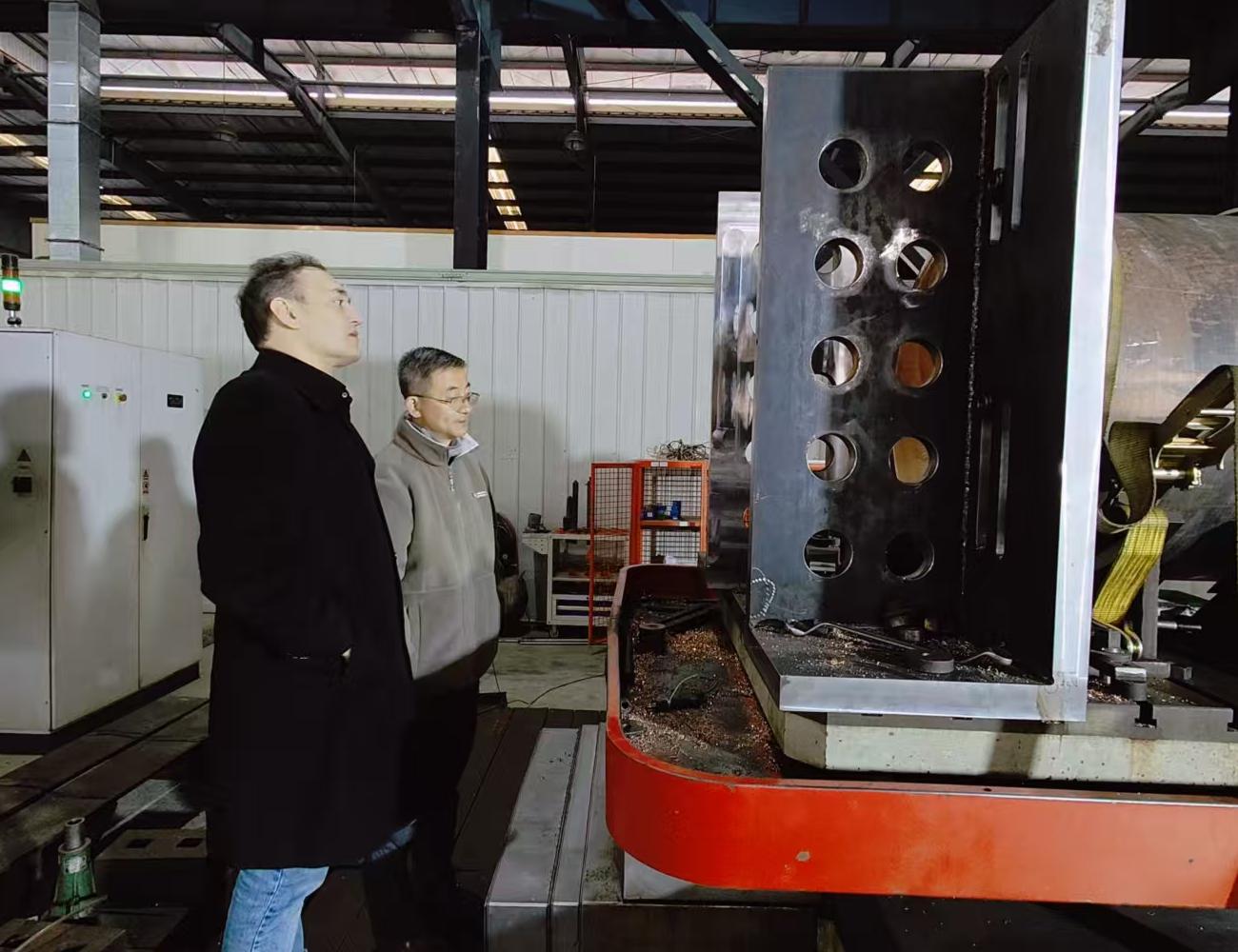
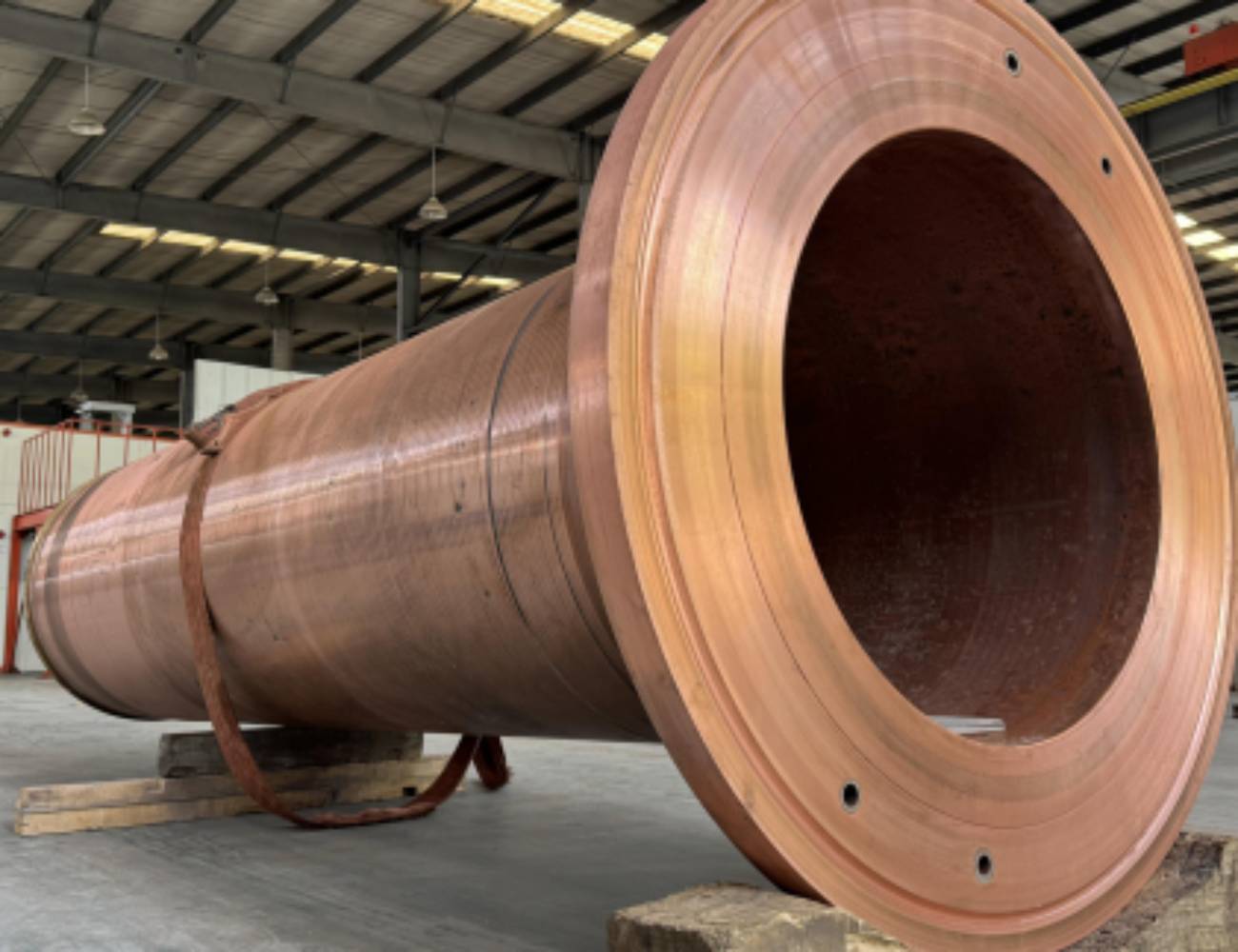
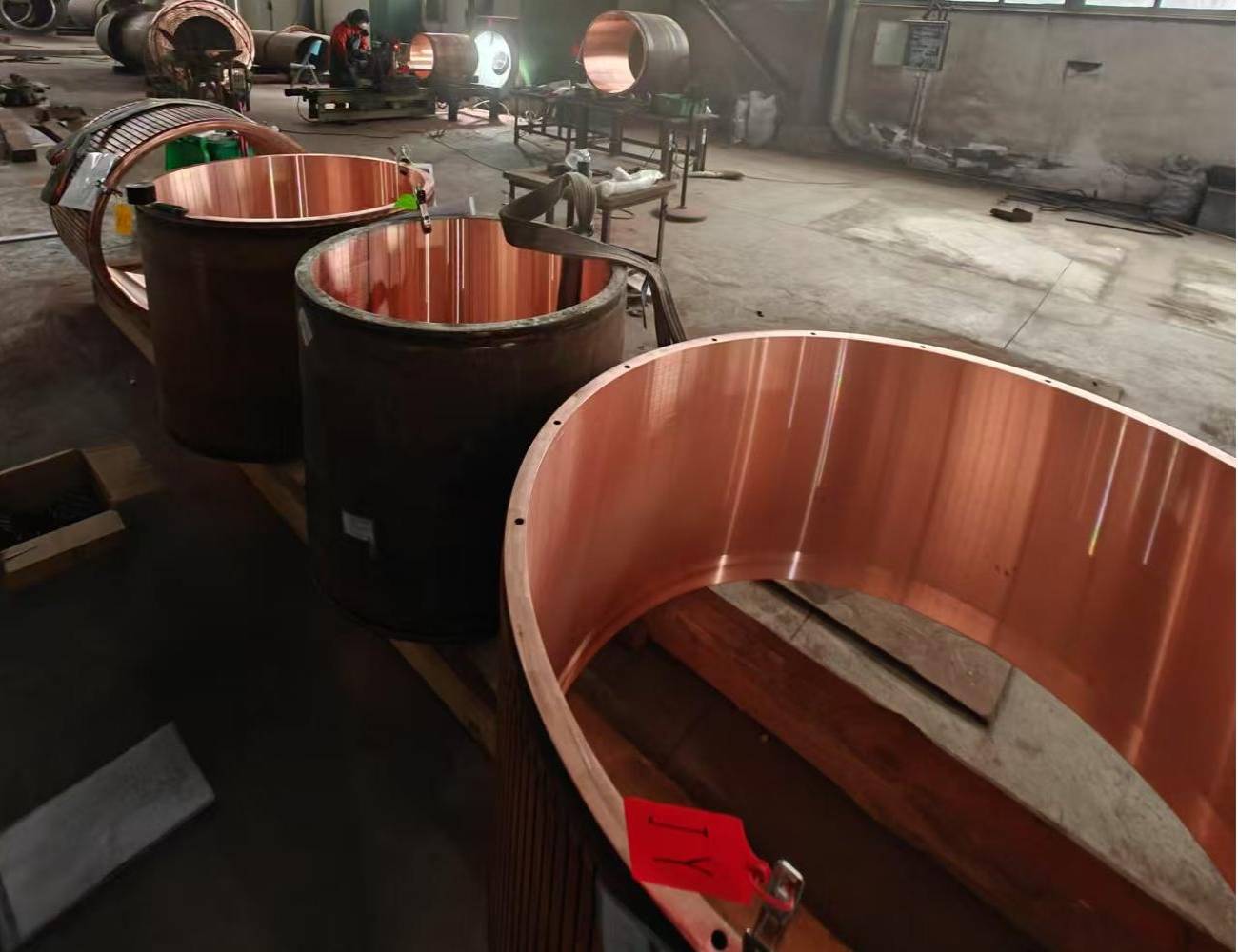
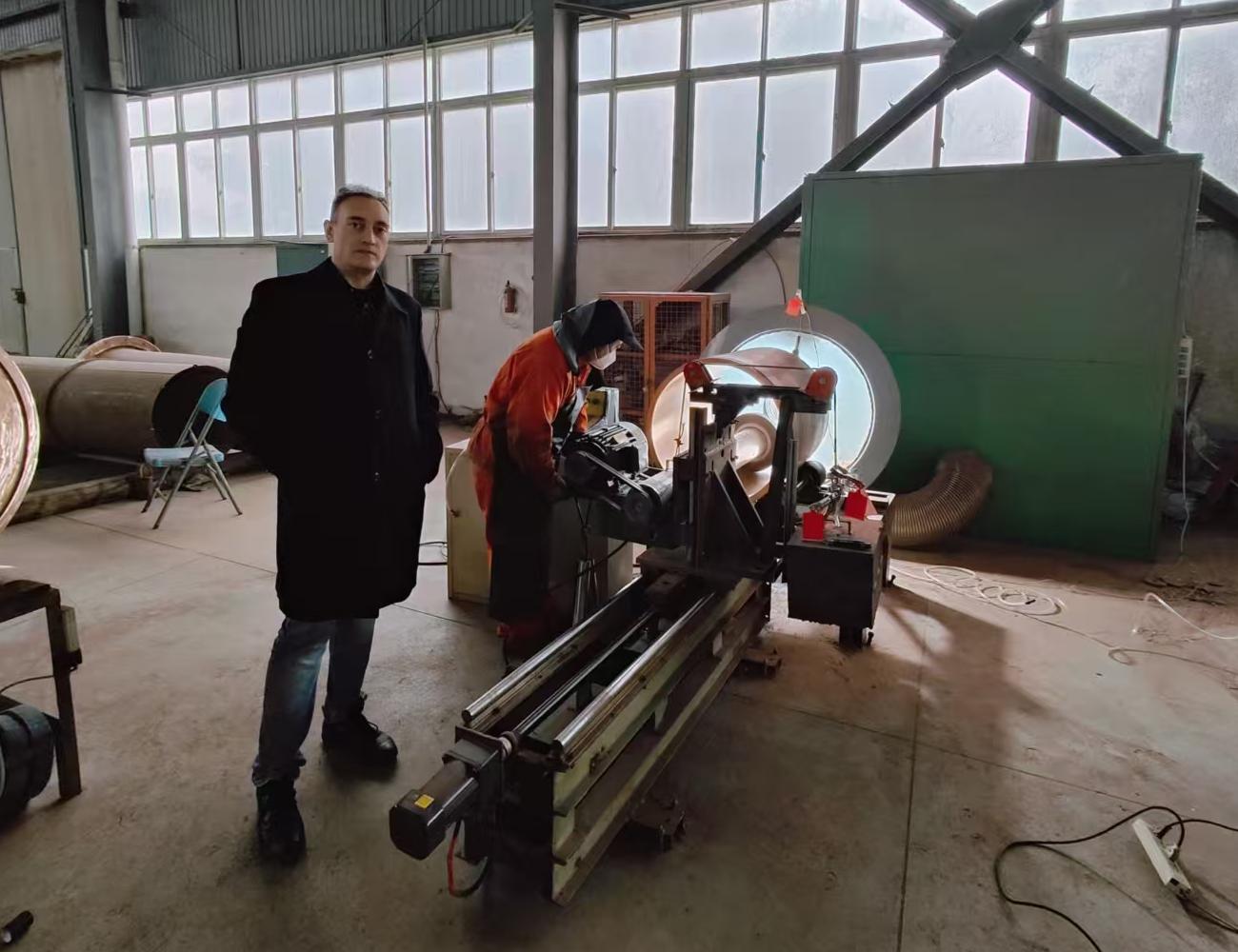
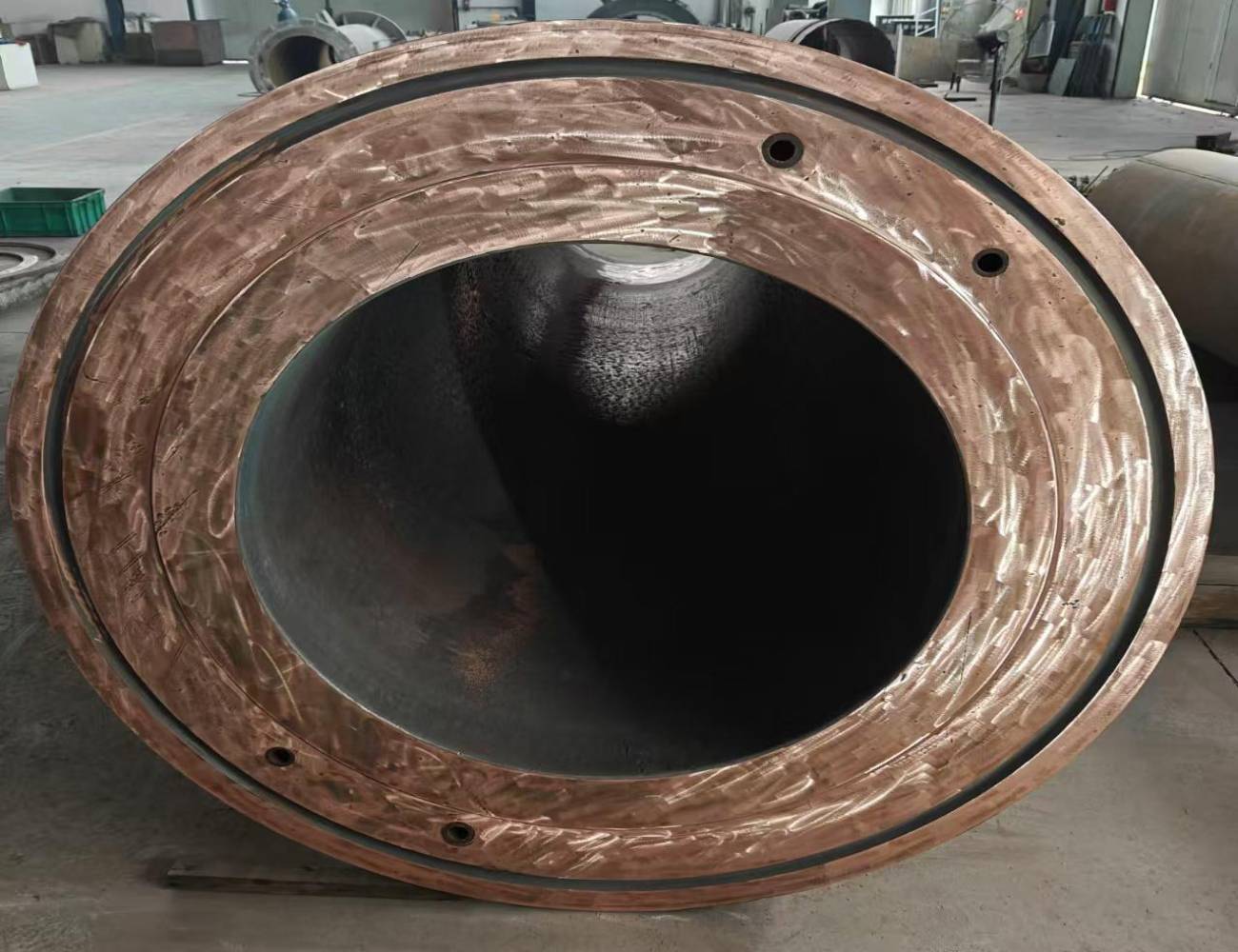